by
Esther Mar
| Jan 09, 2018
The following is a quotation from the 1948 edition of the ASM Metals Handbook:
“Any specimen of steel when examined closely enough will reveal the presence of particles of material incongruent with the metal lattice and demonstrating either definite nonmetallic or quasi-metallic properties. Some of these are obviously of foreign origin and are entrained particles of refractory, slag and the like, that have been entrapped by the freezing steel. These are called exogenous, adventitious or accidental inclusions. Others just as evidently have been precipitated from the liquid or solid metal as a result of chemical reactions or of solubility changes caused by varying temperature. Such inclusions are known as indigenous, natural, or native inclusions and must be considered an integral part of the heterogeneous and complex material known as steel. They are as much a part of steel as seeds are part of a fruit.”

These days, along with the popularity of seedless grapes, many steel customers have requirements for steel with a minimum volume fraction of inclusions and length of inclusions. Various properties are adversely affected by inclusions; including impact properties, hot fatigue strength, hot workability, and formability. Especially in forming applications manganese sulphide “stringer” inclusions are detrimental to edge stretching. For such applications steel with “inclusion control” is often specified. It is important to note, however, that this term is not equivalent to “inclusion shape control”. The former requires the steel producer to lower the Sulphur content of the steel whereas the latter requires the steel producer to modify the shape of sulphide inclusions so that they are less damaging. Inclusion control is accomplished through various practices in the refining and continuous casting operations. Inclusion shape control is commonly achieved by calcium treatment.
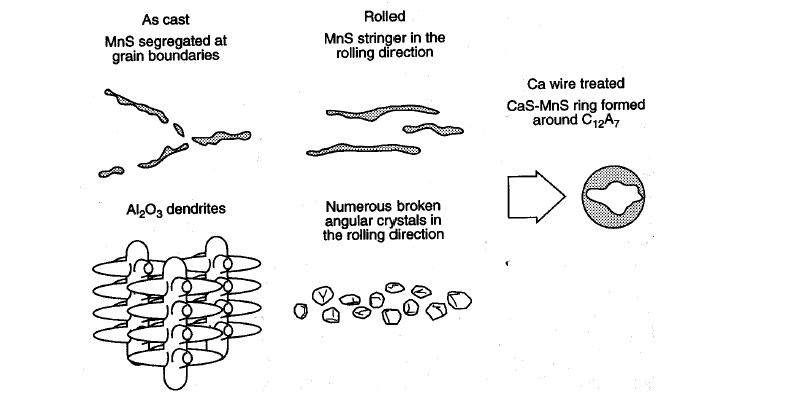
Calcium is generally added to steel in a stabilized form such as calcium silicon, delivered via cored wire, using a wire injection system. This is normally done in the ladle after trim additions and argon rinsing. Calcium is a powerful deoxidizer and desulphurizer and thus has two beneficial effects. The first is that it reduces the total number of inclusion remaining in the steel and the second is that it modifies the shape of the remaining inclusions into more globular ones that are less detrimental to the properties of the final product.
As steelmaking quality has improved “inclusion controlled” steel has become cleaner and often just specifying in this manner is sufficient for many applications. An example of such a specification is ASTM A1011 HSLAS-F (where the “F” designates improved formability). In applications where “inclusion shape control” is known to be required special care must be taken to specify this even where the governing standard does not refer to it.