by
Esther Mar
| Feb 21, 2018
Hot –dip galvanneal and hot-dip galvanize can both be produced on the same continuous coating line. The fundamental steps in the process are:
• Uncoiling a steel coil (usually cold rolled full hard)
• Preparing/cleaning the incoming steel strip
• Annealing
• Applying zinc coating (with a small aluminum level that is lower in galvanneal than galvanize)
• Wiping off excess coating
○ Reheating (in the case of galvanneal production)
• Cooling the strip
• Temper rolling and/or tension leveling
• Applying a surface treatment (e.g. passivation, oil)
• Recoiling
Coating differences
- Galvanize has a zinc coating with a very thin iron/aluminum/zinc bonding layer.
- In manufacturing galvanneal, the objective is to convert the zinc coating to a zinc-iron alloy with a bulk composition of approximately 90% zinc and 10% iron.This is done in a Galvanneal Furnace by reheating the strip in a controlled fashion to between 500 – 600oC, for a few seconds, soon after the wiping knives.The iron diffuses out of the steel into the zinc coating producing 3 layers of inter-metallic phases called Zeta, Delta and Gamma each having an increasing iron content, with Gamma being closest to the steel surface.
Visual differences
- Galvanize has a shiny metallic appearance.
- Galvanneal has a dull gray matte appearance.
Performance differences
- Weldability
- Zinc-iron alloy coatings generally have better spot welding characteristics than pure zinc coatings.The coating has higher electrical resistance, hardness and melting point than a pure zinc coating, allowing welds to be obtained with lower currents with longer electrode life.
- Paintability
- Better paint adhesion is obtained with a galvanneal coating because the paint is mechanically locked into its porous surface.
- Formability
- Galvanize coating is quite soft and is easily scratched.In fact its ductility allows it to act almost as a lubricant in a forming die.By comparison a galvanneal coating is very hard and therefore not as easily scratched when handling.Galvanneal coating can also be stretch formed and drawn under specific conditions and many deep drawn automotive parts are produced from a galvannealed product. The galvanize coating may gall on deformation whereas the galvanneal coating may powder.
- Adherence
- Both products offer excellent adhesion to the steel substrate.
- Corrosion Performance
- The corrosion performance of galvanized steel is directly related to the thickness of the coating.
- The corrosion performance of galvannealed steel is not normally compared to galvanized steel because most of the applications are painted after fabricating.Coating thickness also plays a part in the corrosion protection of galvanneal.
In summary whether to use galvanize or galvanneal depends on the demands of the specific application.
Galvanized Steel
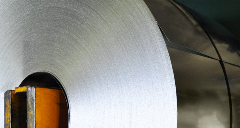
Galvannealed Steel
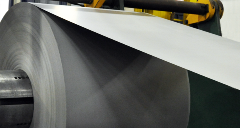